

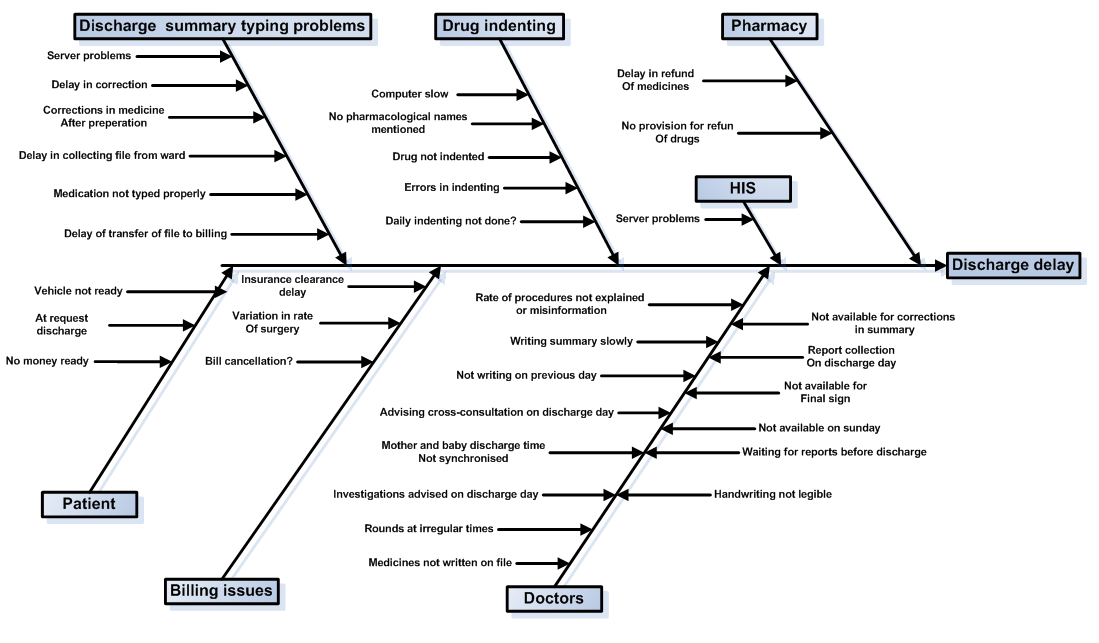
Helps develop in-depth joint brainstorming discussionĬomplex issues may lead to a messy diagram Irrelevant potential causes can cause confusion Helps identify cause and effect relationships For example, if you complete a fishbone diagram and it has 40 potential causes, the team will be left feeling like the problem is too big to handle. This usually leads to a low success rate because hardly any team has the resources to fix every potential cause. The brainstorming process can produce irrelevant potential causes along with relevant ones, which can result in confusion and a time drain.Ĭomplex diagrams with multiple factors can lead to a jumbled mess that is too difficult to display in a fishbone diagram.įishbone diagrams can lend themselves to the divergent approach – the temptation to identify and fix everything that might be causing the problem. Some disadvantages that can present themselves relate to the greatest strengths of the fishbone diagram. Help prioritize relevant causes, so underlying root causes are addressed first. The process of asking why something happened repeatedly at each stage helps drill down to one or more root causes, The brainstorming process encourages broad thinking, keeping teams from limited thinking patterns that can lead to getting stuck, Help facilitate joint brainstorming discussions, Help identify cause and effect relationships with underlying problems, Advantages go in accordance with the purpose and method of the diagram.
EXAMPLE ISHIKAWA DIAGRAM HOW TO
Variation in that process usually means variation in the final product.įishbone diagrams are a great tool to either determine potential variables in a process to mitigate defects or failures, or to figure out what’s causing a defect or failure that is currently occurring.Īdvantages and Disadvantages of Fishbone DiagramsĪs we dive into when and how to use a fishbone diagram, it’s important to note the advantages and disadvantages that can present themselves when using this root cause analysis tool. Once an order has been placed, a predictable and standardized process should be followed through to delivery. In nearly any industry or business, variation is quality’s and efficiency’s kryptonite.
EXAMPLE ISHIKAWA DIAGRAM DRIVERS
Details down to the design of the car’s doors, so drivers could rest their arm on it while driving, were considered.
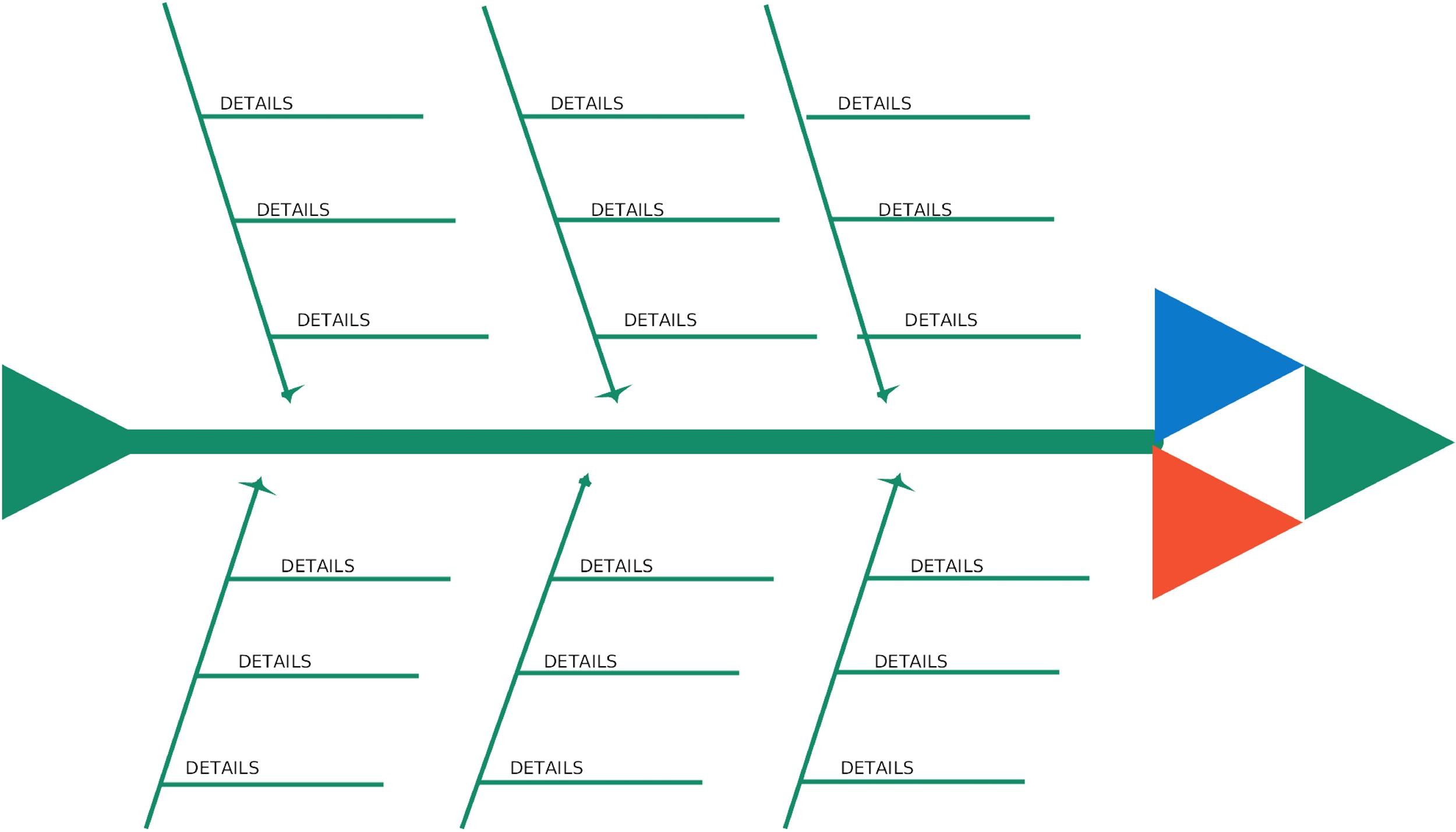
Mazda Motors used fishbones diagrams to design the Miata (MX5) sports car. One of the more famous uses of the fishbone diagram wasn’t used to find causes of existing problems, but rather in the design phase to prevent problems. The concept of the fishbone diagram is said to have been around since the 1920s, but it was popularized by Japanese professor of engineering, Kaoru Ishikawa, who, most notably, put into place the quality management processes for the Kawasaki shipyards. The construction of the fishbone can branch off to as many levels as is needed to determine the causes of the underlying problem. These causes mimic the bones of the fish skeleton. The underlying problem is placed as the fish’s head (facing right) and the causes extend to the left as the bones of the skeleton the ribs branch off the back and denote major causes, while sub-branches branch off of the causes and denote root causes. Sometimes called an Ishikawa diagram or cause-and-effect analysis, a fishbone diagram is one of the main tools used in a root cause analysis.Ī fishbone diagram, as the name suggests, mimics a fish skeleton. In other words, it helps break down, in successive layers, root causes that potentially contribute to an effect. A fishbone diagram is a cause-and-effect discovery tool that helps figure out the reason(s) for defects, variations or failures within a process.
